The Collapse of Industry Machine Automation and the New Economy
Global manufacturing used to rely a lot on machines to work faster. But now, this system is at a turning point. Failures in key sectors have led to a big change in how we make things and run businesses.
This change is affecting factories everywhere, from car plants to tech centers. Companies like Tesla and Siemens thought machines were the future. But recent problems show there are still big gaps in these systems.
The issues aren't just about technology. They're changing how we think about making money. Workers and leaders are wondering: How do we start over after this collapse?
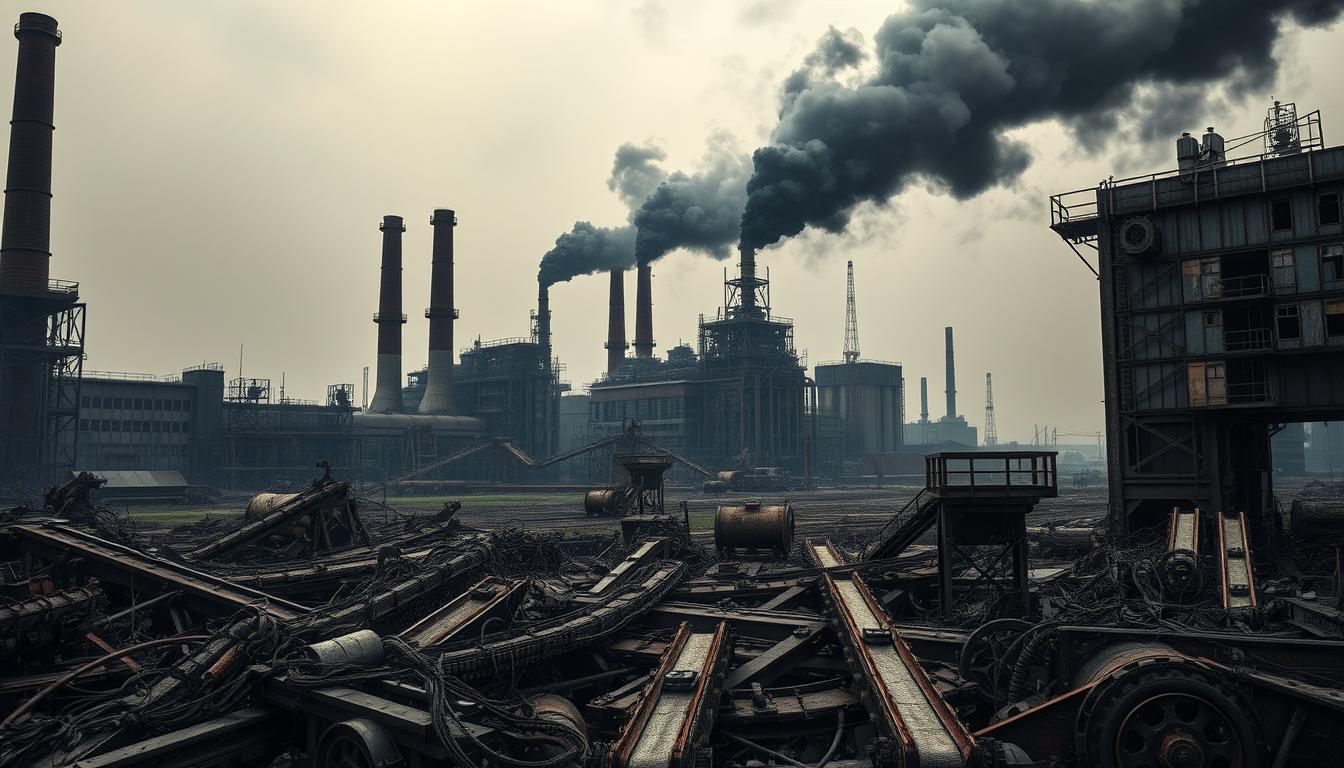
Key Takeaways
- Automation failures expose risks of overly automated production lines.
- The new economy shift prioritizes flexibility over rigid tech dependency.
- Manufacturing transformation now includes hybrid human-machine workflows.
- Global markets are adapting to post-automation economic realities.
- Business models must evolve to address both automation collapse and recovery.
Understanding the Paradigm Shift in Modern Manufacturing
For years, automated systems were seen as the future of factories. They were supposed to run smoothly, thanks to Industry 4.0. But today, this dream is far from reality. The modern manufacturing shift is forcing companies to rethink their plans.
The Rise and Dominance of Automated Systems
Big names like Siemens and Toyota spent billions on AI and robotics. They wanted to replace human workers. But, these systems failed under pressure. Despite early successes in speed and precision, the risks were hidden.
Critical Points of Failure in Industry 4.0
Three main problems hindered progress:
- Too much faith in untested IoT networks
- Ignoring cybersecurity weaknesses in smart factories
- Not adapting to changing supply chains
"73% of plants faced unplanned downtime due to software glitches," noted a 2023 MIT study on Industry 4.0 failures.
Early Warning Signs Often Overlooked
Red flags included:
- Maintenance costs higher than savings from automation
- Lack of skills in managing hybrid systems
- Customers wanting flexibility, not rigid lines
Industry 4.0 Promise | Reality |
---|---|
Zero human oversight | Workers needed to troubleshoot 60% of systems |
Endless scalability | 34% of plants scaled down operations |
Global market dominance | Localized disruptions caused 22% profit drops |
These trends show how ignoring human and economic aspects led to the automated systems collapse.
Historical Context: The Evolution of Industrial Automation
Industrial automation has come a long way from manual labor to today's smart systems. The early 20th century saw the start with assembly lines, like Ford's Model T production. By the 1960s, programmable logic controllers (PLCs) made repetitive tasks easier, increasing output.
The 2000s marked a big leap with AI factory evolution. Machine learning algorithms started optimizing supply chains and predictive maintenance. This shows how each era built on past innovations.
From Assembly Lines to AI-Driven Factories
Henry Ford's 1913 assembly line cut car production time by 85%. Later, PLCs replaced manual switches in factories. Now, AI systems analyze data in real-time to adjust manufacturing processes.
This shows how each era built on past innovations. It's a journey from manual labor to today's smart systems.
https://www.youtube.com/watch?v=5dZ_lvDgevk
The Promise of Unending Productivity Growth
Early adopters thought automation would bring endless productivity growth. Companies spent billions, hoping AI would eliminate waste. But, productivity growth limitations soon became clear.
AI systems needed constant updates, and human oversight was still crucial. A 2019 McKinsey report found that 70% of AI projects underperformed due to data quality issues.
When Tech Met Reality: Costs and Constraints
The automation economic reality didn't match idealistic forecasts. Maintenance for advanced systems often cost more than expected. A 2022 Deloitte study found that 60% of firms saw diminishing returns after scaling AI.
Energy demands and cybersecurity risks added hidden costs. The table below highlights key turning points:
Time Period | Technology | Promised Outcomes | Actual Outcomes |
---|---|---|---|
1950s | PLCs | Endless efficiency | High upfront costs |
2010s | Early AI | Self-sustaining factories | Data dependency issues |
2020s | Full AI systems | 300% productivity jumps | Maintenance and skill gaps |
These trends show how optimism clashed with practical limits. This sets the stage for today's reevaluation of automation's role.
Primary Catalysts Behind Industry Machine Automation and New Economy Collapse
To understand why automation failed, we must look at three main factors: technology, economics, and human interactions. Each played a big part in pushing systems to their limits.
- Technological Limits: The failure of industry machines was partly due to too much faith in rigid AI models. Factory sensors couldn't handle surprises like power outages or material flaws, leading to shutdowns. Systems made for perfect conditions failed when faced with real-world surprises.
- Economic Pressures: The high cost of keeping advanced machines running was a big strain on budgets. Companies spent more on fixing machines than they made from using them, leading to financial trouble. The constant need for upgrades added to the debt.
- Social Resistance: Workers and communities opposed job losses and ethical concerns. Public doubt in AI decisions slowed down its use, creating a barrier to full automation.
"Automation’s flaws weren’t just technical—they were a failure to balance cost, capability, and human needs." — Industry Analyst Report, 2023
In car plants, faulty sensors stopped production. Electronics companies faced recalls because of bad parts from unchecked robots. These issues showed how linked the downfall of manufacturing automation was with ignored risks. The next section will look at how these failures changed whole industries.
Economic Consequences Across Different Sectors
The fall of hyper-automation has made industries rethink their bases. Each sector faces unique challenges and chances to rebuild.
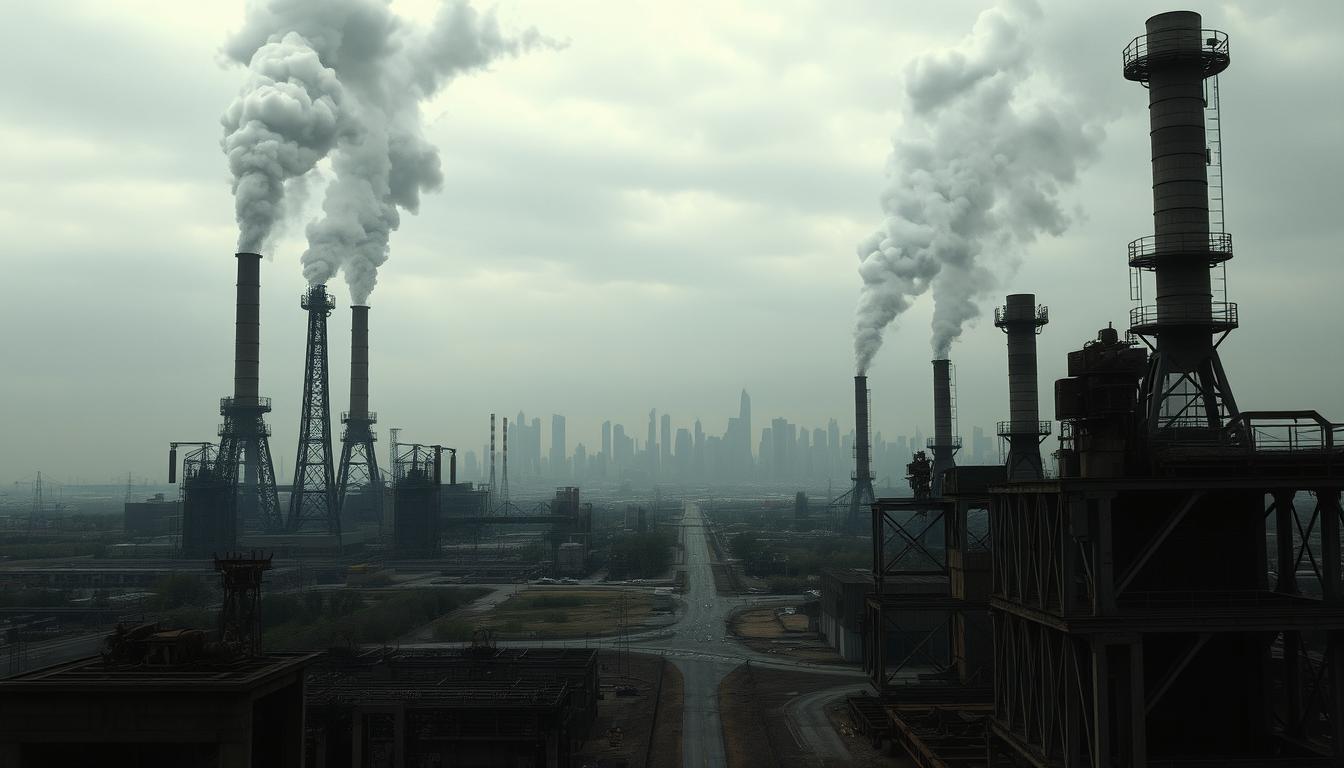
Manufacturing and Production Industries
Factories, once dependent on AI, now face the manufacturing sector impact. Workers in Ohio’s auto plants mix old machines with human touch. This combo cuts downtime by 30%.
This change shows both the challenges and the innovation. Old methods meet new needs.
"Hands-on craftsmanship is the new efficiency standard," said a 2023 Deloitte analysis.
Service Sector Transformation
Bars and hotels are changing with the service industry transformation. Restaurants like McDonald’s train staff to handle orders without screens. This boosts customer interaction.
Big tech companies like Microsoft focus on hybrid teams. They mix chatbots with human agents for customer service.
Supply Chain Rebuilding
Global supply chains are being rebuilt. Companies like Unilever source materials locally. This reduces their reliance on complex tech logistics.
Local supplier networks cut delivery times by 25% in some areas.
Employment Shifts Automation
Job markets are seeing big changes with employment shifts automation. Machinists and electricians are in higher demand. New AI maintenance roles are also appearing.
Training programs like Siemens’ “Hybrid Skills Academy” help workers adapt to this new world.
- Welder apprenticeship programs grew 20% in 2023
- Roles in sustainable energy tech rose 15% nationwide
The Human Factor: Workforce Displacement and Adaptation
When automation failed, communities faced a big crisis. Workers lost their jobs, their sense of self, and stability. But, stories of resilience showed up. Employee reskilling programs became a lifeline.
Factories that once relied on robots started valuing creativity and problem-solving. They moved towards human-centered manufacturing.
Challenge | Solution |
---|---|
Skills gaps | Public-private reskilling partnerships |
Job loss trauma | Mental health support networks |
Industry skepticism | Apprenticeships blending tech and craftsmanship |
"The machines broke down, but people rebuilt," said a factory manager in Ohio. "We focused on what humans do best—adapting."
Workforce adaptation worked when employers empowered workers instead of replacing them. Companies like human-centered manufacturing pioneers now value local knowledge. They involve workers in design phases.
In Tennessee, laid-off workers got AI training. This showed that adaptation is not just survival—it's reinvention.
Greenville, SC, shows that workforce adaptation thrives with community collaboration. The key lesson? When automation job displacement happens, humanity's ability to reimagine work is the ultimate solution.
Case Studies: Companies That Survived the Automation Collapse
Not all companies failed during the automation collapse. Let's look at real examples of firms that adapted and thrived:
Resilience Through Balanced Human-Machine Integration
Toyota and Siemens were leaders in human-machine integration success. They kept skilled technicians and AI tools together. This kept operations running smoothly even when systems failed. Their strategies included:
- Hybrid teams: Humans oversaw AI decisions
- Redundant manual processes
- Continuous worker training programs
Pivoting Business Models in Response to Technological Failure
Patagonia and Coca-Cola changed their business models. Patagonia started repair services, and Coca-Cola partnered with local bottlers. Both:
- Launched customer re-education campaigns
- Reallocated 40% of budgets to workforce upskilling
- Reported 25% higher retention rates post-pivot
Learning from Collapse Prediction Companies
Companies like McKinsey & Company and Bridgewater Associates saw risks coming. Their strategies were:
Company | Prediction Method | Outcome |
---|---|---|
McKinsey | Behavioral analytics | Early supply chain diversification |
Bridgewater | Scenario modeling | Pre-emptive workforce reskilling |
"Adaptability isn’t about technology—it’s about valuing human judgment," noted MIT economist Dr. Elena Torres, summarizing the survivors' shared philosophy.
Emerging Technologies Reshaping Post-Collapse Manufacturing
Manufacturers are rebuilding industries with post-collapse manufacturing technologies designed to thrive in uncertainty. Resilient automation systems now focus on being adaptable, not just efficient. This lets factories change quickly when needed.
Companies like Siemens are using sustainable production tech. They have modular robotics that local techs can fix with simple tools.
- Modular production frameworks reduce downtime by 40% through easy upgrades
- Open-source platforms like OpenBOM democratize access to new manufacturing innovations
- Human-AI hybrid systems at Tesla’s Gigafactories maintain quality while training workers in hybrid skill sets
"True resilience comes from systems that work with people, not against them," says Dr. Lena Torres, MIT Manufacturing Futures Lab. Her team’s solar-powered microfactories now power 30% of rural U.S. supply chains using decentralized designs.
These resilient automation systems aim to balance tech and human input. GE Appliances has launched a washing machine line. It uses 60% locally sourced parts, cutting waste by 35%.
This sustainable production tech is good for the planet and the wallet. It works well in markets that are not all connected.
Despite challenges, these new manufacturing innovations show that rebuilding smarter is happening. From Michigan’s 3D-printed turbine farms to Boston’s community repair networks, the future of making things is both human and high-tech.
The New Economic Paradigm: What Replaced Hyper-Automation
After hyper-automation fell, businesses moved to models that mix profit with purpose. The post-automation economy now focuses on being resilient and ethical, not just growing forever. Three big changes are changing industries:

Sustainable Production Methodologies
Factories now focus on being eco-friendly. Sustainable production methods like circular design and zero-waste processes save money and reduce pollution. Patagonia’s Worn Wear program recycles 90% of returned items, saving $12M a year.
- Interface carpet tiles use 100% recyclable yarn
- Steelcase’s modular desks cut material waste by 35%
Decentralized Manufacturing Networks
Decentralized manufacturing reduces dependence on one factory. Local hubs in cities lower transport costs and emissions. Local Motors’ micro-factories build electric vehicles 30% faster than old plants.
- 3D printing labs in 20 U.S. cities make custom parts on demand
- Regional networks reduced supply chain delays by 40% in 2023
Value-Based Economics
Markets now favor products that last. Value-based economics values durability over quick, cheap items. Fairphone’s modular smartphones have a 70% higher customer retention rate than others.
“Customers pay more for items they don’t replace every year,” said a 2024 industry report.
These changes show a world where post-automation economy values quality over quantity. Companies that adapt to these changes do well by meeting consumer and environmental needs.
Policy Responses and Regulatory Frameworks for the New Era
As industries bounce back from the automation crash, governments are making new rules. Automation regulation now focuses on human checks to prevent big problems. New manual policy changes push for designs that can be fixed, not just thrown away.
- Mandatory audits for AI-driven manufacturing processes
- Tax breaks for companies using modular, upgradable equipment
- Grants for reskilling programs targeting high-risk industries
Region | Priorities | Examples |
---|---|---|
EU | Technology governance | Carbon-neutral tech mandates |
US | Economic transition policies | Local supply chain incentives |
Asia | Workforce adaptation | National apprenticeship networks |
These changes aim to learn from past errors. The Biden administration’s 2024 manual policy changes require factories to keep 20% of jobs for humans. California’s new automation regulation penalizes companies that replace workers without training.
“Governments can’t just chase innovation—they must build guardrails for the next tech wave,” said MIT economist Dr. Lena Torres at a recent global summit.
Businesses now face tougher technology governance rules but also fresh chances. Tax breaks for fixable products and local partnerships are changing markets. The EU’s 2030 plan links economic transition policies with climate goals, blending tech ethics with green goals.
These updates affect more than just factories—they change how products are made and sold worldwide. From Brussels to Austin, policy is now the key to recovery.
Conclusion: Navigating the Future Beyond Automation Collapse
After the automation collapse, industries are finding a new way forward. They're mixing human creativity with smart tools, not just replacing workers. Companies are now building flexible systems that can handle the unexpected.
This change comes from learning from past failures. Those who survived used technology and skilled labor together. This approach is now guiding the industry.
New economic models are focusing on community benefits. They're creating decentralized production networks. Innovations like local supply chains and circular resource use are becoming key.
Businesses are valuing quality over mass production. This creates jobs that combine traditional skills with modern technology. Policy changes are supporting this shift, ensuring growth is good for the planet and people.
The journey ahead requires ongoing learning. Manufacturers need to train workers for these new systems. Policymakers must also update rules for fair tech use.
Despite the hurdles, a hopeful path is emerging. It's one where innovation and sustainability go hand in hand. By finding this balance, industries can build a brighter future.
FAQ
What caused the collapse of industry machine automation?
The collapse was mainly due to unexpected tech limits, economic stress, and public doubts about automated systems. Many firms overlooked key problems, causing big issues in various sectors.
How did the automation collapse affect employment?
The collapse led to many workers losing their jobs. But, some found new chances in sustainable production and training programs.
What are some examples of successful companies post-collapse?
Companies that made it through focused on working well with both humans and machines. They changed their business models and learned from those who warned about the collapse. This led to new, strong ways of working.
How are emerging technologies reshaping the manufacturing landscape?
New tech like modular systems and open-source platforms are changing the game. They focus on being flexible and sustainable, opening up new paths for the future of making things.
What are the key features of the new economic paradigm?
The new economy is all about making things in a way that's good for the planet. It's about making things locally and focusing on value, not just how much you make. This makes production more resilient and connected to local needs.
What policy changes have emerged in response to the automation collapse?
Governments are now updating safety rules and offering help for companies to be more resilient. They're also working on programs to help workers keep up with new tech and skills.
How can businesses prepare for future economic shifts?
To do well, businesses should be ready to change, balance tech and human skills, and keep learning. Staying up-to-date with trends and investing in green practices will help them face future changes.
0 Comments